Case Studies
Key Points for Reliably Improving the Precision of Additive Dosing
Industry:
Resin manufacture
Department:
Research and Development
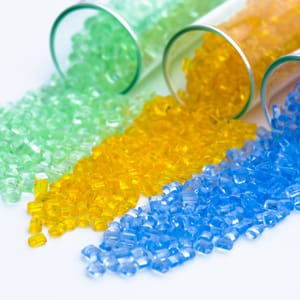
Background
The manufacturer featured in this case study was trying to break into the functional resin market with plastics for consumer applications. When it provided a prospective client with a prototype, however, the client raised quality issues, which the manufacturer would need to resolve as soon as possible if it was to move closer to its goal of breaking into the market.
Problem
Client Demands Tolerances of ±1.0%
The issues raised with the prototype concerned the precision of additive dosing. While the client demanded a dosing precision of ±1.0%, analysis of the prototypes found a variance of ±3%— a dosing accuracy of ±1.0% is generally not very demanding for materials used in high-performance resins. The research and development team(R&D) began considering ways of achieving the precision target. The employee who was in charge recalls:
“We attempted by trial and error to improve dosing precision using our existing equipment. However, because of the hard-to-handle nature of the additives, which are prone to bridging, we were unable to achieve sufficiently accurate dosing. At the same time, we also tried to gather information on competitors in the high performance resin industry, but were unable to come up with anything useful concerning manufacturing equipment.”
He became increasingly anxious.
Summary of the problem
High-performance resin manufacturer client required that additives be dosed with a precision of ±1%.
The additives in question were prone to bridging and the manufacturer’s existing equipment was unable to achieve the required dosing accuracy.
While the manufacturer tried to obtain information from other functional resin manufacturers, it did not come up with anything useful.