Case Studies
State-of-the-Art Feeders Boost Productivity Even in Small Numbers
Industry:
Performance resin manufacture
Department:
Production engineering
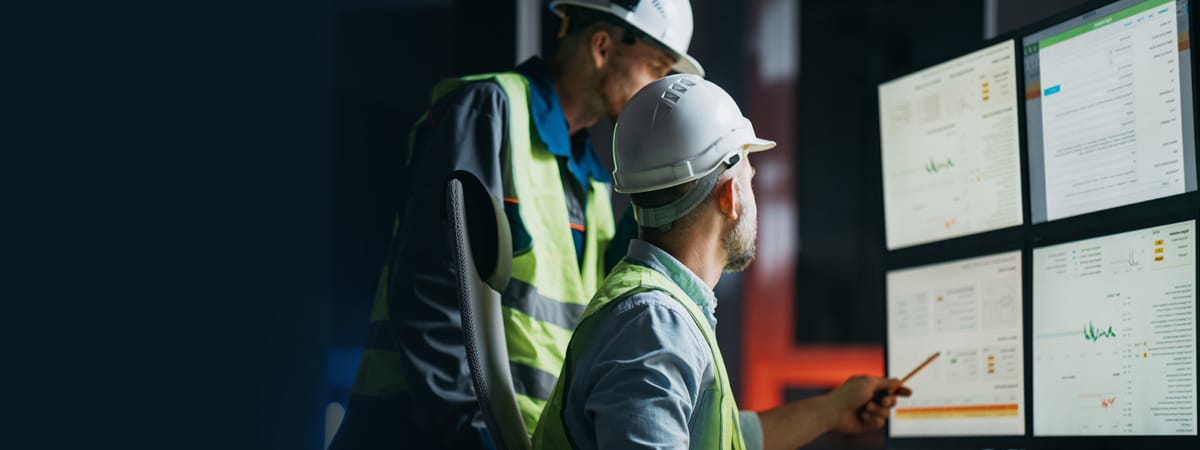
Background
The compound manufacturer featured in this case study was building a new factory to cater to increasing demand for automotive components. However, when the manufacturer commissioned an external consultant to advise it on production line design, the consultant’s investigation uncovered several issues.
Problem
New Factory Perfect Opportunity to Redesign Convoluted Production Lines
When advising on the new factory, the consultant raised several issues regarding existing production lines. Because the manufacturer used a separate production line for each of the compounds that it produced, line output varied from month to month, and some lines had been temporarily shut down. Different lines were also fitted with different feeder types, which meant that each feeder required different consumables, maintenance personnel, and spare parts, creating significant cost. The fact that a large number of production lines had been crammed into a small factory also made the product flow more complex.
The head of the production engineering division was troubled by the consultant’s findings.
“Initially I just thought we could reproduce the production lines in the existing factory. In fact, we were going to have to completely overhaul production line design at the new factory,” she says.
At the same time, the existing production lines were quite old, and the manufacturer lacked the necessary expertise to design new ones from scratch. Inquiries with the company that manufactured the existing feeders did not yield useful replies either. The production engineering team was at a loss to know what to do.
Summary of the problem
The manufacturer operated a separate production line for each compound it produced, and variations in production volumes meant that some lines lay idle.
Because different feeder types were installed on different lines, different consumables, maintenance personnel, and spare parts had to be provided for each feeder type.
Many lines were crammed into a single factory, making for complex product flow.
The manufacturer wanted to resolve the production line issues in the new factory but lacked expertise in production line design.