Case Studies
Rechargeable Battery Component Manufacturer Struggled to Find Right Feeder for New Factory
Industry:
Rechargeable battery component manufacture
Department:
Production engineering
Support from feeder specialist promised reduced overall costs.
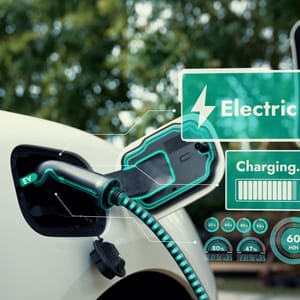
Background
The manufacturer featured in this case study manufactures rechargeable battery components at its base in East Asia. So it could ramp up production and keep up with the high popularity of electric vehicles, the manufacturer had decided to build a big new factory.
Problem
Engineers Wanted to Replace Problematic Feeders but Cost-Conscious Managers Needed Convincing
The most important consideration for the new factory was increasing capacity by ensuring that production lines ran smoothly. The cost-focused approach employed by management meant that the main contender was a feeder of the same model used at the manufacturer’s existing factory. However, the existing feeders presented several challenges. An employee from the production engineering team recalls:
“Firstly, the feeders’ complex design and the need to fit many optional attachments made maintenance costly and time-consuming. Recent advances in battery technology also necessitate very precise dosing, something that is beyond the abilities of our existing feeders. Furthermore, because the company that makes the feeders lacks expertise on the unique specifications of battery components (required to prevent metal contamination and wear), it has struggled to provide appropriate solutions in the past.”
Because failure to resolve these issues could jeopardize future production, the production engineering team wanted to replace its existing feeders with different make. While the employee and her colleagues had approached multiple manufacturers, a feeder with the right balance of cost and performance eluded them. With management still not convinced, time dragged on, and before the team realized, the deadline for ordering the equipment for the new factory was upon them.
Summary of the problem
- The existing feeders’ complex design and need to fit many optional attachments made maintenance time-consuming.
- The feeders’ lack of precision meant they could not keep up with advances in battery technology.
- Because the company that made the feeders lacked the relevant expertise, it was unable to provide solutions suited to the unique specifications of battery components.
- The engineering team wanted to replace the existing feeders, but cost was an issue.