Case Studies
Solves the Challenges Presented by Rechargeable Battery Manufacture
Industry:
Rechargeable battery manufacture
Department:
Production engineering division
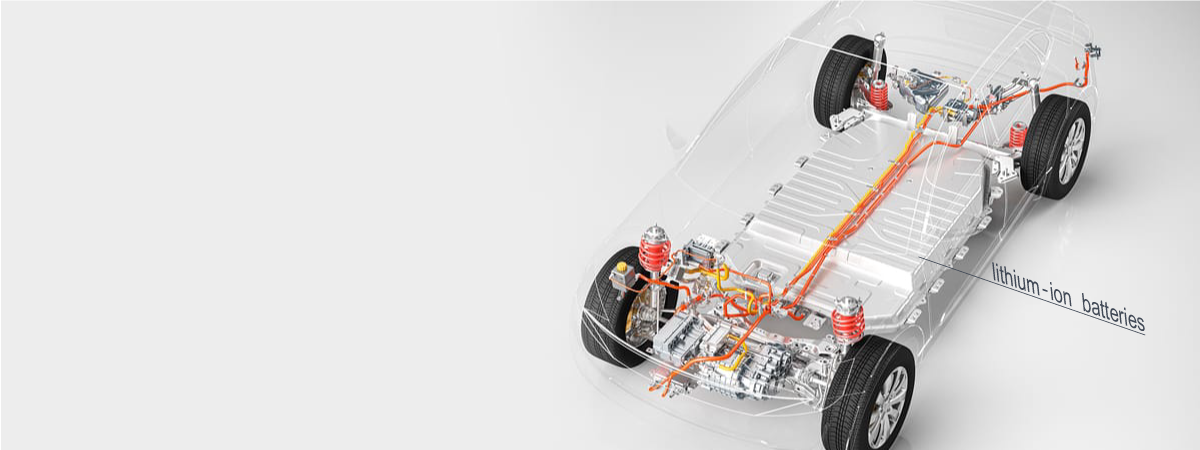
Background
The manufacturer featured in this case study produces anodes for lithium-ion batteries, which are increasingly in the spotlight as drivers transition to electric vehicles. As lithium-ion battery technology is still in its evolution, it is not unusual for a material that was used on the production line in the past to be replaced overnight with a completely different one. This manufacturer was no exception, and was required to switch to a new material (lithium iron phosphate) at the request of the battery manufacturer.
Problem
"If only there was a universal feeder suitable for production lines with ever-changing materials."
When the supplier set about deploying lithium iron phosphate on the production line by way of a trial, it found that its traditional feeders were completely unsuitable: the lithium iron phosphate would leak out between gaps in feeder components. Because the material was extremely prone to flushing, the supplier needed to design a brand-new production line could handle lithium iron phosphate.
After performing a detailed investigation of the properties of the material in response to these issues, the production engineering division realized that it faced many challenges.
The member of the team who was charged with handling this matter recalls:
"Lithium iron phosphate, being prone to flushing, contains minuscule particles and is highly fluid, so if it becomes aerated during filling, the powder can overflow from the hopper and leak from the clamp. Lithium iron phosphate was the complete opposite of the bridge-prone material we used previously, which tended to stick to the walls of the feeder, causing ‘rat-holing’: a void would form in the hopper while the material remained stuck to the walls of the feeder."
That was not the only issue. The factory became contaminated with lithium iron phosphate, causing production lines used for other products to be affected. The leakage had also caused measuring errors, affecting production plans. Furthermore, the employee found that lithium iron phosphate is mildly toxic, therefore creating the risk that manufacturing staff would suffer health issues. This material required a hermetic feeder.
"Properties-wise, materials used in rechargeable batteries, including lithium-ion batteries, tend to be much more difficult to handle as they are more prone to bridging and flushing than other chemicals. However, because rechargeable battery technology is currently evolving, I believe that the frequent switching of materials will remain a requirement."
In the mid-to long-term, a single feeder that was suitable for both bridge-prone and flushing-prone materials would have been ideal. However, neither the employee nor anyone else on her team knew of such a universal feeder. Meanwhile, time ticked on with no progress being made.
Summary of the problem
Lithium iron phosphate is prone to flushing and leaking.
Leaked lithium iron phosphate would contaminate that the factory, creating health risks.
The new feeder needed to be able to handle both bridge-prone and flushing-prone materials.