Case Studies
Upscaling Challenges Prompt Manufacturer's Continuous Process Transition
Industry:
Rechargeable battery manufacture
Department:
Production engineering division
We look at how one manufacturer significantly boosted its production volume by improving critical processes.
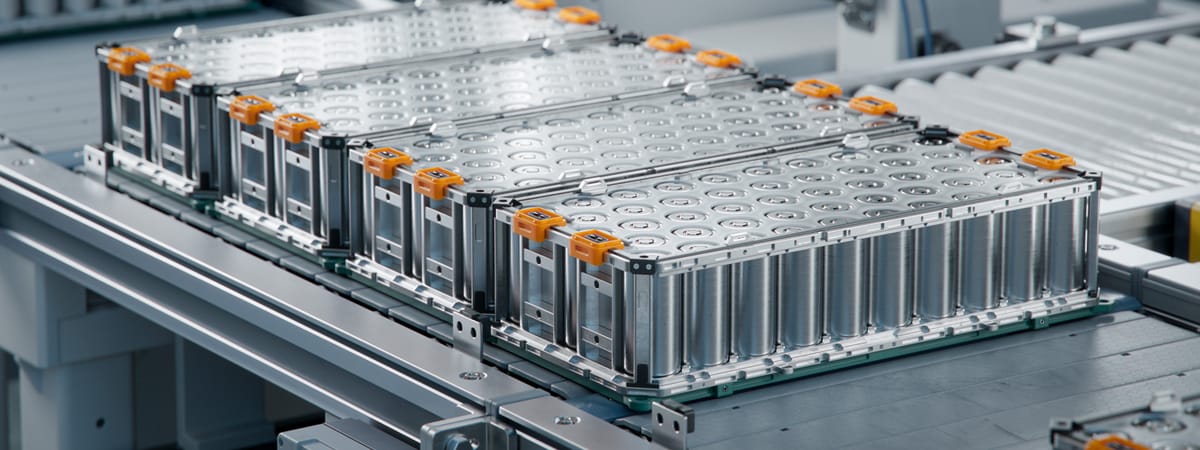
Background
Increased demand for rechargeable batteries for electric vehicles meant that the manufacturer featured in this case study had been running its production lines at full capacity for months. However, just when the manufacturer decided to boost capacity significantly to cater to additional demand, it encountered a problem.
Problem
Attempt to Transition to Continuous Process while Minimizing Risk Creates Many Challenges
The production engineering team that was assigned the task of reviewing the plan to increase production capacity believed that dosing and mixing were the most important processes performed on the existing anode production line. The project leader recalls.
“We used to use a batch process for manufacturing anodes whereby powdered chemicals were measured in set quantities and mixed all at once. While batch mixing processes allow the size of the mixing tank to be increased when upscaling production, in this case, the need to uniformly mix multiple materials with different particle sizes and specific gravities, we could not make the tanks any larger,“ he says.
The team also felt that retaining the existing batch approach would not allow increases in productivity due to the personnel requirements associated with reconfiguring the production line between products and transporting mixtures between processes. It was this that made the team leader interested in a continuous approach to anode production.
“The industry was transitioning from a batch-based approach to a continuous one, which allows for reduced staff numbers and much better productivity. This prompted us to decide to switch to a continuous anode manufacture process as well,“ says the team leader.
However, obtaining information on competitors' technologies has proven challenging, given the highly confidential nature of technologies used in the rechargeable battery industry. Additionally, concerns about product traceability in the event of quality issues and the need to minimize risks associated with the transition to a continuous process have also been raised.
Summary of the problem
With the existing batch process used to manufacture anodes, there was a limit to the extent to which upscaling would translate into increased productivity.
Transitioning to a continuous process was therefore key to boosting productivity, but it was difficult to obtain information on the necessary equipment.
There were also concerns about the continuous production system, such as traceability in the event of defects.